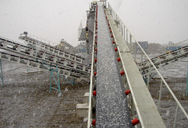
Ball Milling - an overview | ScienceDirect Topics
Ball milling technique, using mechanical alloying and mechanical milling approaches were proposed to the word wide in the 8th decade of the last century for preparing a wide spectrum of powder materials and their alloys. In fact, ball milling process is not new and dates back to more than 150 years. It has been used in size comminutions of ore, mineral dressing, preparing talc powders and many ...
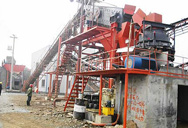
Ball Milling - University of Massachusetts Boston
Real-time Analysis for Pollution Prevention ... Ball milling should be considered as a potentially attractive solution for solvent-free synthesis. 21 Solvent free One-pot process Tip of iceberg . Reference Lance Frazer, Environmental health perspectives, 2003, 111, 10 Belen Rodríguez, Adv. Synth. Catal. 2007, 349, 2213 Ana Lazuen Garay, Chem. Soc. Rev., 2007, 36, 846–855 Raphael Janot ...
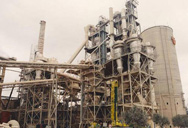
Ball mill - Wikipedia
Ball milling boasts several advantages over other systems: the cost of installation and grinding medium is low; it is suitable for both batch and continuous operation, similarly it is suitable for open as well as closed circuit grinding and is applicable for materials of all degrees of hardness. Varieties. Aside from common ball mills there is a second type of ball mill called a planetary ball ...

Mechanochemical deconstruction of …
3.2. Micromorphology characterization analysis during ball milling 3.2.1. Field-emission scanning electron microscopy (FE-SEM) images. To better understand the impact of mechanical fragmentation on the micromorphology properties of stone stover, SEM combined with AFM was carried out in this study.

189 questions with answers in BALL MILLING | …
25.03.2020 · Dear All, I am facing a problem during ball milling that the Pure aluminum with 15 % Alumina by volume reinforcement is becoming reactive in open air after 24 hours of ball milling.
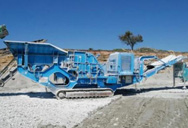
(PDF) Residual Stresses Analysis in Ball end …
7 Residual Stresses Analysis in Ball end Milling of Nickel-Based Superalloy Inconel 718 Figure 9. Residual stress pro les for di erent feeds, (a) σ xx , (b) σ yy , ( a p =0.3mm, a e =0.2mm, V e ...
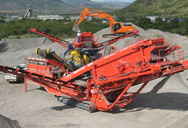
Synthesis of Nanomaterials by High Energy Ball …
It is a ball milling process where a powder mixture placed in the ball mill is subjected to high-energy collision from the balls. This process was developed by Benjamin and his coworkers at the International Nickel Company in the late of 1960. It was found that this method, termed mechanical alloying, could successfully produce fine, uniform dispersions of oxide particles (Al

Ball Mill: Operating principles, components, Uses ...
A ball mill also known as pebble mill or tumbling mill is a milling machine that consists of a hallow cylinder containing balls; mounted on a metallic frame such that it can be rotated along its longitudinal axis. The balls which could be of different diameter occupy 30 -50% of the mill volume and its size depends on the feed and mill size. The large balls tend to break down the coarse feed ...

EFFECT OF BALL SIZE DISTRIBUTION ON MILLING PARAMETERS
2.6.2 Milling performance of a ball size distribution 40 2.7 Summary 41 Chapter 3 Experimental equipment and programme 43 3.1 Laboratory grinding mill configuration 43 3.2 Preparation of mono-size grinding media 44 3.3 Feed material preparation 46 3.3.1 Coal sample collection at Tutuka power station 46 3.3.2 Feed preparation for laboratory tests 46 3.4 Experimental procedures 47 3.4.1 ...

MODULE #5: FUNCTIONAL PERFOMANCE OF BALL MILLING
In rod milling, you can use work index analysis to relate design and operating variables to overall circuit efficiency. However, you cannot use work index analysis for the same purpose on ball mill circuits because of the complex interactions between grinding and classification. In this module, you will learn how to relate design and operating variables to ball mill circuit efficiency through ...

Effect of ball milling energy on rheological and …
Statistical analysis. Significance of the effect of ball milling energy on rheological and thermal parameters of modified amaranth stone were evaluated by one-way ANOVA (significance level α = 0.05 %) with Tukey post-test using Prism 5 (GrapPad Software Inc., San Diego, CA, USA).
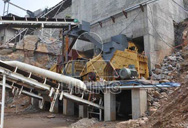
Ball Mill - RETSCH - powerful grinding and …
RETSCH is the world leading manufacturer of laboratory ball mills and offers the perfect product for each application. The High Energy Ball Mill E max and MM 500 were developed for grinding with the highest energy input. The innovative design of both, the mills and the grinding jars, allows for continuous grinding down to the nano range in the shortest amount of time - with only minor warming ...

Mechanical Milling: a Top Down Approach for the Synthesis ...
ball milling as a non-equilibrium processing method which can be analogous to rapid solidification. This review will first describe the equipment and some of the process va-riables used for high energy ball milling. Next, the physics of the milling processes has been described to the extent that it is presently understood, and models of the mechanics of several mills has been reviewed. An ...

FRITSCH Sample Preparation and Particle Sizing - …
FRITSCH IS AT YOUR DISPOSAL - even in difficult times The entire world is holding its breath due to the Corona virus and currently presents us all with new challenges. We remain positive and will do everything to ensure that your contact persons continue to be available as usual, whether in Idar-Oberstein, from the home office or worldwide.

Debromination and Decomposition Mechanisms …
Ball-milling experiments were carried out by using a planetary ball mill (YXQM-2L, MITR Instrument Equipment Company, Changsha) . A mixture of nonmetallic particles and iron powder (1.20 g in total) was placed in the grinding pot with agate balls (5–10 mm in diameter). The total weight of the balls was approximately 180 g. The iron powder was ball-milled with nonmetallic particles in ...

High-energy ball milling technique for ZnO …
29.04.2011 · Therefore, conventional ball milling system cannot be used directly to conduct any HEBM work and specially designed ball mills with a higher milling energy are preferred for HEBM.43. Lattice relaxation of ZnO in z direction observed in our study has also been reported by a number of workers. For example, Bao et al44 reported on the observation of slightly higher c values for ZnO thin films ...

Functional Performance Analysis Of Ball Milling - …
Functional Performance Analysis Of Ball Milling. We are a large-scale manufacturer specializing in producing various mining machines including different types of sand and gravel equipment, milling equipment, mineral processing equipment and building materials equipment. And they are mainly used to crush coarse minerals like gold and copper ore, metals like steel and iron, glass, coal, asphalt ...

Practical 1 : Ball Milling | TF Lab 1
23.12.2013 · Practical 1: Title: Ball Milling Objective: To grind the coarse salt to a smaller size by using a ball mill and to obtain the particle size distribution of the initial and the sieved final mixture. Introduction: Ball milling is a method used to break down the solids to smaller sizes or into a powder. A…

Functional Performance Analysis Of Ball Milling
MILLING &ANALYSIS OF PARTICLES AUTUMN 2010. milling). The milling tools (also called grinding media) are located in a closed vessel and are accelerated by the movements of the vessel or by a stirring mechanism. The relative movement of the milling tools strains the milling good in between. 3.2 Ball mills Ball mills are the most important group ...