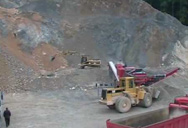
Sintering: A Step Between Mining Iron Ore and …
Sintering: A Step Between Mining Iron Ore and Steelmaking By Alison Cestari 06.11.2019 The USGS defines iron ore as a mineral substance which, when heated in the presence of a reductant, will yield metallic iron (Fe).
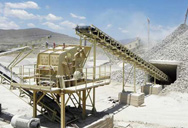
Modeling Sintering Process of Iron Ore - IntechOpen
Modeling Sintering Process of Iron Ore Jose Adilson de Castro Graduate Program on Metallurgical Engineering -Federal Fluminense University Brazil 1. Introduction In this chapter, a methodology for simulating th e sintering process of iron ore is presented. In order to study the process parameters and inner phenomena, a mathematical model based on transport equations of momentum en ergy and ...
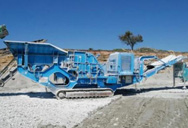
(PDF) Iron Ore Sintering: Process - ResearchGate
Sintering is a thermal agglomeration process that is applied to a mixture of iron ore fines, recycled ironmaking products, fluxes, slag-forming agents and solid fuel (coke).
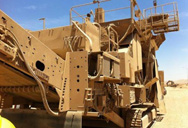
What Is Iron Ore Sintering? (with pictures)
02.04.2020 · Other iron ore sintering processes use machines that take crushed iron ore and mix it with water and other substances, known as fluxes, prior to igniting the mixture. Electricity is conducted through the mixture, and its surface is ignited to help form an agglomerate. Dust from the iron ore, as well as iron particles that do not meet size requirements, are recirculated through the machine …

Iron Ore Sintering: Process - researchgate.net
Sintering is a thermal agglomeration process (1300-1480°C, Eisele and Kawatra, 2003) of a mixture of iron ore mineral fines (0.5-8 mm), by-products of the iron and steelmaking industry,
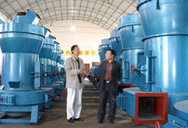
The Sintering Process of Iron Ore Fines – IspatGuru
Sintering process helps utilization of iron ore fines (0-10 mm) generated during iron ore mining operations. Sintering process helps in recycling all the iron, …
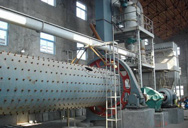
Iron Ore Sintering: Process: Mineral Processing …
17.05.2017 · Sintering is a thermal agglomeration process that is applied to a mixture of iron ore fines, recycled ironmaking products, fluxes, slag-forming agents, and solid fuel (coke). The purpose of the sintering process is manufacturing a product with the suitable characteristics (thermal, mechanical, physical and chemical) to be fed to the blast furnace. The process has been widely studied and ...
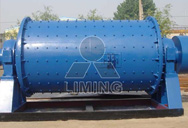
The Relationship Between Mining and Sintering
The Relationship Between Mining and Sintering By Alison Cestari 08.15.2019 Sinter is the primary feed material for making iron in a blast furnace, and we have previously written about sintering and how it is a step between mining ore and steelmaking. The only source of primary iron is iron ore, but before all that iron ore can be turned into steel, it must go through the sintering process ...

Iron Ore to Sintering to Steelmaking - Analyzing …
But before all that iron ore can be turned into steel, it must go through the sintering process. Sinter is the primary feed material for making iron and steel in a blast furnace. We recently wrote about sintering in our sister blog, Advancing Mining. Read the article to learn more about how sinter quality begins with the mined iron ore and the proper selection and mixing of the raw materials.
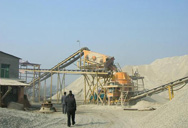
Sinter plant - Wikipedia
Sinter plants agglomerate iron ore fines (dust) with other fine materials at high temperature, to create a product that can be used in a blast furnace. The final product, a sinter, is a small, irregular nodule of iron mixed with small amounts of other minerals. The process, called sintering, causes the constituent materials to fuse to make a single porous mass with little change in the stone properties of the ingredients. The purpose of sinter are to be used converting iron into steel.
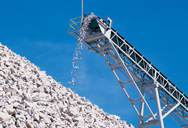
CHAPTER-11 FUNDAMENTALS OF IRON ORE SINTERING
CHAPTER-11 FUNDAMENTALS OF IRON ORE SINTERING R. P. Bhagat INTRODUCTION The process of sinter making originated from a need to make use of fines generated in mines and in ore benefiCiation plants. With the development of sintering technology, a sintering plant has become a tremendous success for providing a phenomenal increase in productivity and saving in coke rate to …
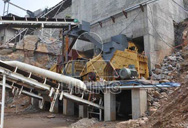
Iron-process sintering of iron ores - YouTube
30.09.2012 · As-mined iron ore contains lumps of varying size, the biggest being more than 1 metre (40 inches) across and the smallest about 1 millimetre (0.04 …
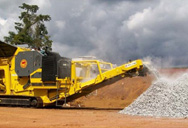
Iron ore mining and dressing - tec-science
Regions in which iron ore has formed over millions of years (e.g. through volcanism) and can be mined economically are also referred to as iron ore deposits. Especially many ore deposits can be found in countries such as China, Australia, Brazil, India and Russia. These countries account for around 85 % of the total global iron ore mining volume.
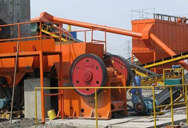
Iron processing | Britannica
Iron processing, use of a smelting process to turn the ore into a form from which products can be fashioned.Included in this article also is a discussion of the mining of iron and of its preparation for smelting. Iron (Fe) is a relatively dense metal with a silvery white appearance and distinctive magnetic properties. It constitutes 5 percent by weight of the Earth’s crust, and it is the ...
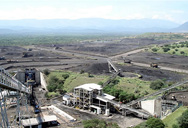
Iron ore sintering - ScienceDirect
Like other sintering processes, iron ore sintering converts iron ore fines of often − 8 mm sizing into larger agglomerates, namely, sinter, between 5 and 50 mm particle size, which possess the physical and metallurgical characteristics and gas permeability required for efficient blast furnace operation.
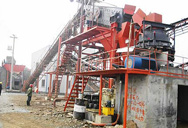
Iron Ore Agglomeration Processes and their …
History of sintering of iron ore. Middle of nineteenth century, small sintering pot used to be constructed in the copper mining in England. The origin of sintering process goes back to 1887 when F. Haberlein and T. Huntington of England invented the process of agglomeration for sintering of sulphide ores. In this process, the sintering was ...
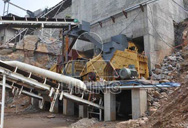
091102 Iron ore - European Commission
Metal ore (including sulphide ore) roasting or sintering, including pelletisation 13.10 Mining of iron ores Information on the number of iron ore and concentrates production installations in the EU 27 that are included in the ETS has been provided by Euromines 3. An overview of the installations is given in Table 2. Table 2 Overview of EU27 installations included in the ETS (Euromines, 2009 ...
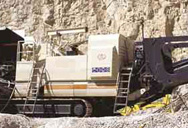
Optimising iron ore sinter leads to cost savings - …
A top-tier mining company approached us to get a better understanding of how iron ores with different alumina-containing minerals influence the sintering process. Enlarge image We simulated industrial sintering using advanced x-ray diffraction techniques, revealing the mineralogical changes that occurred as a function of temperature and time for each ore type.
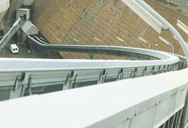
Iron ore sinter and sinter making Part 2 - YouTube
10.05.2016 · The presentation describes sinter plant, its major equipments, its operation, sintering process and the technological developments.