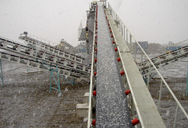
Ball Milling - an overview | ScienceDirect Topics
Ball milling technique, using mechanical alloying and mechanical milling approaches were proposed to the word wide in the 8th decade of the last century for preparing a wide spectrum of powder materials and their alloys. In fact, ball milling process is not new and dates back to more than 150 years. It has been used in size comminutions of ore, mineral dressing, preparing talc powders and many ...
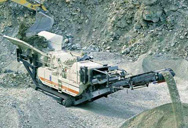
Factorial Experimental Modelling of Ball Milling Response ...
Factorial Experimental Modelling of Ball Milling Response for Baban Tsauni (Nigeria) Lead-Gold Ore. E ... ball milling output increased with increase in grinding time, ball mass to ore sample mass ratio and very slowly with increase in mill speed. The response decreased with increase in ball size. This work established a model for selecting the parameters required for a desired size reduction ...
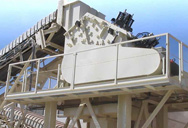
Ball Milling Experiments
Abstract in this work, factorial ball-milling experiments have been applied to bi 2 te 3 material, for the first time, aiming to investigate the effect of the main process parameters on the structural features and thermoelectric properties of the ball-milled materialshe selected main parameters were the duration of milling, the speed, and the ball-to-material ratio. Experiments Based On Ball ...

Factorial Experimental Modelling of Ball Milling …
Factorial Experimental Modelling of Ball Milling Response for Baban Tsauni (Nigeria) Lead-Gold Ore - written by E. A. P. Egbe published on 2013/05/01 download full article with reference data and citations
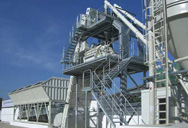
Ball Milling | Material Milling, Jet Milling | AVEKA
Ball milling is a size reduction technique that uses media in a rotating cylindrical chamber to mill materials to a fine powder. As the chamber rotates, the media is lifted up on the rising side and then cascades down from near the top of the chamber. With this motion, the particles in between the media and chamber walls are reduced in size by both impact and abrasion. In ball milling, the ...
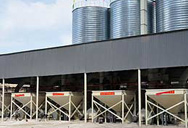
Ball Milling - University of Massachusetts Boston
ball milling Ar c Franziska Schneider, Org. Proc. Res. & Develop., 2009, 13,44 Up to 96% yield Entry Rpm T (min) Yield% 1 400 10 92 2 800 5 94 . Aldol Condensation 17 B. Rodr´ıguez, Angew. Chem., Int. Ed., 2006, 45, 6924 O + H O R (S)-proline 10 mol% Ball milling (A) or stirring (B) H R Entry R= Method t/h Yield% anti/syn ee% 1 4-NO 2 A 5.5 99 89:11 94 2 4-NO 2 B 24 95 89:11 94 3 3-NO 2 A 7 ...
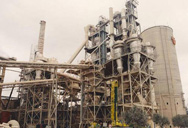
Ball mill - Wikipedia
Ball milling boasts several advantages over other systems: the cost of installation and grinding medium is low; it is suitable for both batch and continuous operation, similarly it is suitable for open as well as closed circuit grinding and is applicable for materials of all degrees of hardness. Varieties. Aside from common ball mills there is a second type of ball mill called a planetary ball ...
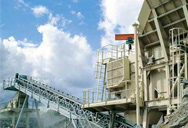
Study of the process of stirred ball milling of …
Factorial design enables analysis of process parameters as independent variables. This tool is especially efficient for complex systems with multiple variables and responses, such as ball mills. The statistical computation provides a quantitative overview of the process parameters on the basis of a restricted number of experiments. In the present study the variables are rotation speed of the ...
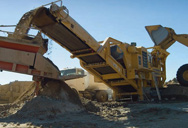
Effect of ball milling energy on rheological and …
Pearled amaranth grains obtained by abrasive milling were processed by planetary ball milling to produce amaranth flours. The influence of milling energy on rheological and thermal behavior of amaranth stone dispersions and stability during 24 h storage at 4 °C were investigated based on a factorial design. The rheological behavior of stone dispersions (4 % and 8 % w/v) was determined …
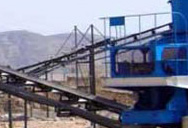
(PDF) Study of the process of stirred ball milling …
Study of the process of stirred ball milling of poorly water soluble organic products using factorial design Article (PDF Available) in Powder Technology 198(1):56-60 · February 2010 with 376 Reads
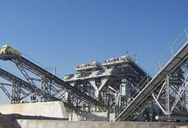
How can one select ball size in ball milling and …
There should be atleast 25% empty place in the milling jar after feeding balls and the material while high energy impact. There is no such thumb rule for powder to ball ratio.
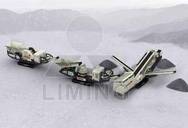
Optimization of ball milling parameters for processing Fe ...
A factorial design statistical analysis has been used in order to obtain the optimum parameters of the high energy ball milling process to obtain Fe-50%atSi alloy. The optimum parameters were with respect to ball milling energy, i.e., milling time and rotation speeds. The correlation between these parameters and the final content of FeSi compound for Fe-Si powder mixture were developed with ...
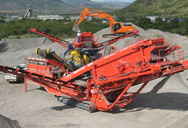
Micronization of a Soft Material: Air-Jet and Micro …
24.11.2010 · In comparison, a lab scale air-jet mill was used at various milling parameters according to a full factorial design, where the response factors were particle yield and particle size distribution, which was analyzed using laser diffraction and scanning electron microscopy. The yield achieved with the micro-ball mill was 100% but was ~80% for the air-jet mill, which reduced the size of Pluronic ...